Experimental parameters of salt spray corrosion test machine
The salt dry-wet composite salt dew corrosion tester tests the salt spray corrosion resistance of electroplating and paint decoration layers of automotive parts, building materials, coating electrical appliances, electrical machinery, and other equipment.
As a modern technology enterprise integrating R&D, manufacturing, sales, training, and service, our company is committed to delivering more testing instruments to the market, providing testing instruments for textiles, leather, combustion, automotive interior and exterior trims, material environmental climate aging, etc., and non-standard customization is also acceptable. Before purchase, targeted tests can be carried out according to customer requirements to ensure that the purchased instruments are suitable.
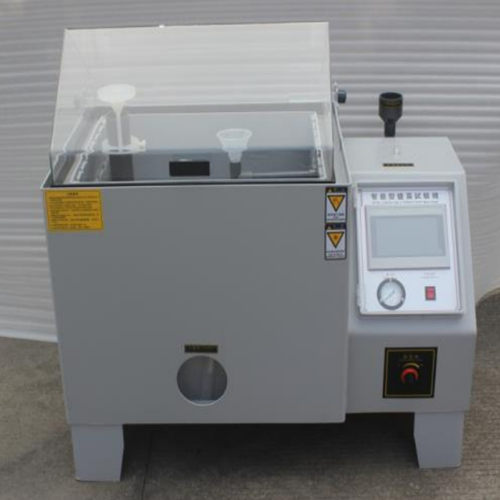
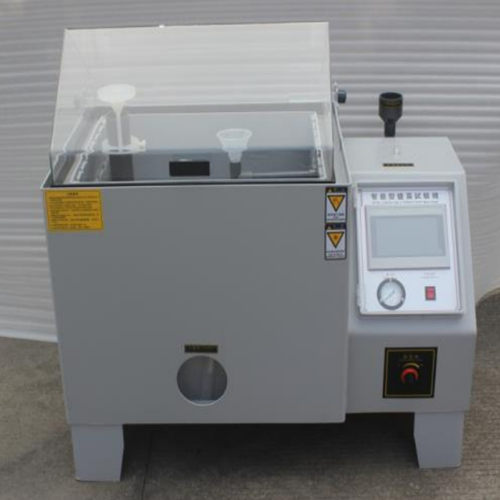
Experimental parameters:
A. According to CNS, JIS, ISO, GJB, and GB specifications, spray test conditions can be set:
1. Salt spray test: NSS, ACSS
* Laboratory: 35℃±1℃.
* Saturated air barrel: 47℃±1℃.
2. Corrosion resistance test: CASS
* Laboratory: 50℃±1℃.
* Saturated air barrel: 63℃±1℃.
B. Spraying method:
a. The salt water is absorbed and then atomized by the Bernoulli principle. The atomization degree is uniform, and there is no blocking and crystallization phenomenon, which can ensure the standard of continuous testing.
b. Nozzle: Made of a special glass nozzle, the spray volume and angle can be adjusted.
c. Spray volume: adjustable to 1~2ml (ml/80cm2/h) (16-hour average volume).
d. Air supply system: The air pressure is 1kg/m² and is adjusted in two stages. The first stage is a rough adjustment and the second is a precise adjustment.
C. Hot air drying test:
1. Test temperature range: room temperature + 10% ~ 70℃ ± 1℃.
2. The air in the temperature box outside the test room is blown by a blower through the air heater and then enters the test room, thereby forming a low-temperature condition in the test room. The temperature of the test room is controlled by the heater in the temperature box. (SSR drive)
D. Wetting test:
1. Test temperature range: room temperature + 10% ~ 60℃ ± 1℃
2. Test humidity range: 60%RH~98%RH.
3. Steam introduction is adopted to generate moisture by heating water, and then introducing it into the test room through the blower. The microcomputer processor of the IPC-1000 controller, which plays the main control role, performs micro-motion control when the humidity reaches the required value. When the humidity exceeds the value, dry hot air is introduced to dilute the moisture and discharge the excess moisture outside the test room. Electronic parallel micro-motion wet system. (SSR drive)
E. Temperature control accuracy in the test chamber:
1. Temperature control accuracy: uniformity ±2℃, fluctuation ±2℃.
2. Humidity control accuracy: uniformity ±3%RH, fluctuation ±2%RH.
Main features:
1. No need to manually move the sample from one test chamber to another.
2. No need for heavy manual salt spraying.
3. Eliminate the test result error caused by multiple sample processing.
4. Simple operation
The cycle is designed under 4 conditions: spray, dry, humidity, immersion, and static (drying function is used at room temperature). These conditions as well as time, temperature, and humidity can be easily controlled by the built-in microprocessor of the test chamber. The universal software allows users to easily select programs and control operations. Users can quickly add new cycle programs or perform any preset cycle program. The timer can set the working time of each functional program or terminate the test. The controller continuously displays the test conditions and the test process.
5. Easy maintenance
The side panels of the box can be removed for direct inspection of the control components. All components are also installed in positions that are convenient for inspection and maintenance. Each test liquid can be directly discharged, the liquid tank is easy to clean, and a test liquid indicator device is attached, which is extremely convenient for inspection during the test. The side and top cover of the test chamber are easy to open, making it easy to place samples in the chamber. The controller has complex self-diagnosis functions, including over-temperature alarm, water shortage alarm, safety self-locking, etc.
6. Safety
All electrical circuits are equipped with ordinary circuit breakers, and ground circuit breakers are also installed. All heaters are equipped with electronic and mechanical overheat protection devices.
7. Imported PP sheet structure
The salt spray test chamber is made of a solid PP sheet. This material has strong corrosion resistance, reliable electrical insulation performance, long service life, UV protection, anti-static, high-temperature resistance, and other properties, and will not cause pollution to the sample. The solid and thick box wall and top cover have low thermal conductivity, which is conducive to accurate temperature control. Higher test temperature than other test chambers.
8. Controlled mist dispersion
Compared with traditional test chambers, the test chamber has a super atomization dispersion effect. While the compressed air regulator controls (spraying distance), the speed-controlled compressor can be used to control the amount of corrosive solution delivered to the sprayer, and the cone regulator can be adjusted to adjust the spray size. The cone regulator can also play the role of refining the spray particles.
9. Built-in liquid reservoir
The test chamber is equipped with a liquid reservoir inside, which improves space utilization and reduces maintenance. It can meet the operation needs of tests for more than three days. The liquid reservoir is also equipped with a salt filter. The spray tank and the immersion tank are relatively independent. The immersion tank can automatically discharge into the test tank and automatically recover the test solution used for immersion from the test tank.
10. Fast cycle
The test chamber has a * box heater and a large capacity dry cooling fan, which can change the temperature very quickly. Its auxiliary air heater ensures dry conditions with very low humidity. Traditional water-jacketed test chambers often cannot change the cycle conditions quickly due to the large heat capacity of water, and cannot produce low humidity conditions at all.
11. Reliability
As standard equipment, the test chamber has an independent alarm processing device, which can ensure the reliability of the test program and will not cause the test conditions to deviate from the standard test method due to interference from the display, diagnosis, or reminder functions of the controller.