The impact of laboratory temperature and humidity conditions on experimental res
As an important performance of textiles, abrasion resistance has a great impact on the wearing function of fabrics and clothing, so it is one of the important assessment indicators for wearing fabrics, and it has also attracted more and more attention from the industry.Flat abrasion resistance testing of woven fabrics is usually carried out using Martindale abrasion testers.
Martindale abrasion tester is used for abrasion resistance and pilling degree test under pressure of woven fabrics, knitted fabrics, woolen fabrics, artificial leather, synthetic leather, etc., and is used in textile, footwear, clothing and other industries.
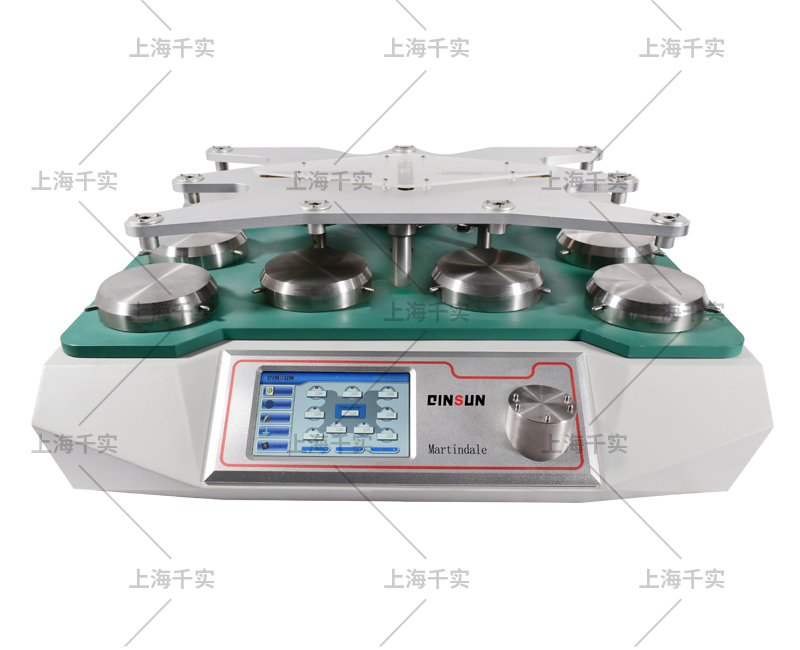
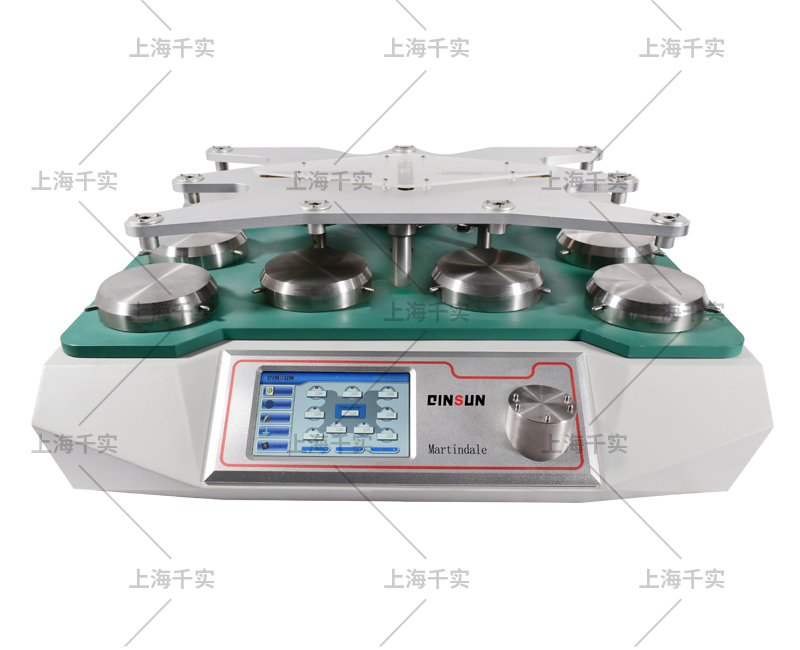
The principle of testing:
1. Circular fabric samples, under a certain pressure, are rubbed against standard abrasives following the Lissajous curve motion trajectory. The number of abrasion cycles until sample damage occurs represents the fabric's abrasion resistance.
2. Circular samples of the same material, under a specified pressure, are rubbed using the Lissajous pattern motion trajectory. After a certain number of rotations, the sample's pilling and fuzzing level is evaluated.
Applicable standards:
GB/T 13775-92 Martindale method for abrasion resistance of cotton, linen, and silk woven fabrics
GB/T 21196.1-2007 Determination of Martindale abrasion resistance for textiles - Part 1
GB/T 21196.2-2007 Determination of Martindale abrasion resistance for textiles - Part 2
GB/T 21196.3-2007 Determination of Martindale abrasion resistance for textiles - Part 3
GB/T 21196.4-2007 Determination of Martindale abrasion resistance for textiles - Part 4
GB/T 4802.2-1997 Martindale pilling test for fabrics
GB/T 8690-88 Martindale method for abrasion resistance of wool fabrics
ISO 12945-2:2002 Martindale method for the determination of fabric surface pilling properties - Part 2
ASTM D 4966-1988 Martindale abrasion testing for fabrics
ASTM D 4970-2002 Martindale method for fabric pilling resistance testing
Additionally, overall, wool woven fabrics have good abrasion resistance, while viscose woven fabrics have poor abrasion resistance, and polyester/cotton blended woven fabrics fall in between. This aligns with the ability of the fibers to withstand repeated stretching. Wool fibers, despite lower strength, have high elongation and elasticity, resulting in better fabric abrasion resistance. Viscose fibers, although stronger, exhibit poor elasticity, leading to lower fabric abrasion resistance. Polyester fibers have high breaking strength and good elasticity recovery, maintaining decent abrasion resistance even in blends with cotton.
Factors affecting the flat abrasion performance of woven fabrics include fiber material, weave structure, warp and weft density, yarn density, fabric thickness, and surface density. Experimental results show the following correlations:
1. Fibers with greater deformation ability during repeated stretching exhibit better fabric abrasion resistance.
2. For loosely woven fabrics with lower warp and weft density, plain weave structures perform well in abrasion resistance. However, for denser fabrics, under similar conditions, twill weave structures outperform plain weaves.
3. Under similar conditions, yarn density, warp and weft density, fabric thickness, and surface density are positively correlated with fabric abrasion resistance.The impact of laboratory temperature and humidity conditions on experimental results is mainly reflected in fibers. Specifically, humidity significantly affects the abrasion resistance of viscose fibers, while it has almost no effect on polyester and acrylic fibers, and has some impact on nylon fibers.