Analysis of the Pilling Property of Cashmere Fabric Detected by ICI Rolling Box
As we all know, fabrics are constantly subjected to various external forces when worn. The continued friction of external forces causes the fluff to entangle into balls and protrude on the fabric's surface. This phenomenon is called fabric pilling. Therefore, when designing fabrics, selecting clothing fabrics, or monitoring fabric quality, attention should be paid to fabric anti-pilling. ICI Rolling Box Pilling Tester is a testing device for detecting the pilling performance of cashmere fabrics. Standard Group (Hong Kong) Co., Ltd. is the manufacturer. Welcome to call for inquiries.
Fabric pilling process:
(a) represents the original fabric;
(b) represents the first stage, the fibers on the surface of the fabric are continuously pulled out of the fabric due to friction to produce fluff;
(c) represents the second stage, the fibers that have not fallen off are entangled with each other, and the pulling of the fibers is aggravated;
(d) represents the third stage, the fibers are entangled more and more tightly, forming small pellets;
(e) represents the fourth stage, the fibers connecting the pellets are broken or pulled out;
(f) represents the fifth state, some pellets fall off.
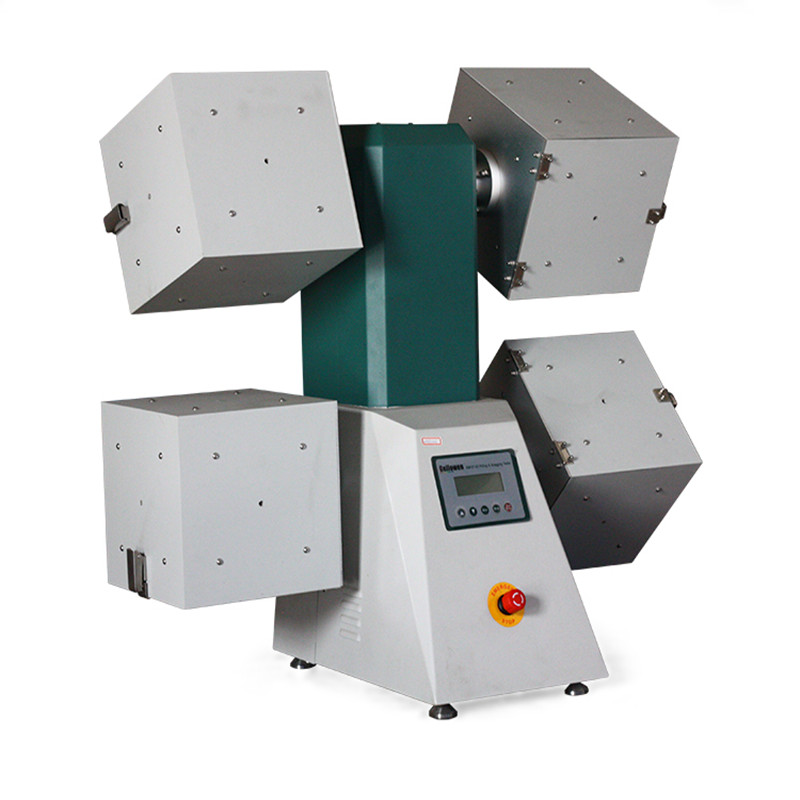
Factors affecting the pilling of cashmere knitwear:
Among the many factors affecting fabric pilling, such as fiber properties, textile process parameters (yarn twist and fabric structure), post-dyeing and finishing, and wearing conditions, fiber properties are the main cause of fabric pilling.
1. Raw material properties
Cashmere fibers are thin and short with a small curl, a nearly circular cross-section, good elongation and elasticity, low bending stiffness, and good fatigue resistance. These properties make the fabric prone to pilling; among them, the short pile rate, length, and length dispersion of the fiber are the main influencing factors. Therefore, in the processing of cashmere products, cashmere raw materials must be reasonably selected according to the performance and use of the product, and combined with other process methods to achieve effective control of cashmere fabric pilling.
2. Spinning twist
For knitted products, under the premise of considering raw material factors, the main factor affecting spinning on pilling is yarn twist. The size of the yarn twist and the ratio of the twist coefficient directly affect the pilling of the fabric. In the yarn twist, the twist of a single yarn determines the degree of cohesion between fibers, and the twist of ply yarn determines the balance of stress in the yarn, so the twist of a single yarn is the key factor in determining pilling.
3. Weaving parameters
For cashmere knitted fabrics, the weaving density is inversely proportional to the coil length. The weaving density of single-sided plain knitted fabrics is small, and the coil length is large. When the fabric surface is rubbed by external force, the fibers in the yarn are subject to less force to prevent them from moving out of the yarn surface, and the fiber ends are easy to extend out of the yarn, increasing the probability of fabric pilling.
4. Dyeing process
During the production process, the dyeing process will affect the indicators of the raw materials. The time, temperature, and pH value of the dyeing process are the three elements to ensure the dyeing quality, but this is also a factor that affects the fiber indicators. When arranging the feeding, the technicians should consider the degree of damage to the raw materials during the dyeing process to make full use of the various indicators of the raw materials. The index values of the raw materials before and after dyeing have changed significantly, the length has decreased, the length dispersion has increased and decreased, and the short pile rate has increased. It can be seen that dyeing has an impact on the raw materials, thereby affecting the pilling performance of the product.
5. Finishing process
The finishing process of cashmere knitwear usually refers to the finishing process that the yarn needs to go through after it is woven into the garment and before it is finished, mainly including milling, special finishing (such as anti-pilling, anti-shrinkage, etc.), and ironing and shaping. Milling is an important part of the finishing process of cashmere knitwear. The main process factors affecting the milling effect are milling agent, bath ratio, temperature, pH value, time, mechanical force, etc. Whether the milling process is reasonable or not directly affects the product's appearance quality, finished product specifications, and pilling performance.
Test method for pilling performance of cashmere products:
Experience shows that when cashmere products are usually tested by Martindale and random drum methods, the results are difficult to reach level 3 or above. For cashmere knitted fabrics, the applicable anti-pilling test method is the IC pilling box method. GB/T 4802.3 (hereinafter referred to as GB), ISO 12945-1 (hereinafter referred to as ISO), and JSL1076A (hereinafter referred to as JIS) methods are compared as follows:
1. Pilling test box
GB and ISO standards have the same provisions on rotating boxes, with a size of 235mm cube, a cork pad thickness of 3.2mm, and no specific requirements on the replacement cycle; JIS standards stipulate that the size is 23mm cube, the cork pad thickness is (3±0.2)mm, the density is (0.25±0.03)g/mm², the tensile strength is 980kPa (10kgf/mm²), and the use limit is 1500 hours. GB and ISO standards do not explain the density, tensile strength, and use limit. The rotation speed specified in the three standards is (60±2)r/min.
2. Polyurethane sample tube
GB and ISO standards have the same regulations on sample tubes, with a tube length of (140±1) mm, a thickness of (3.2±0.5) mm, an outer diameter of (31.5±1) mm, and a mass of (52.25±1) g; JIS standards stipulate that the tube length is 150 mm, the thickness is 3 mm, the outer diameter is 31 mm, the mass is 51 g, and the limit is 47 g. If there is damage, it should be replaced immediately, and the hardness is also stipulated as (42±5).
3. Tape
GB and ISO standards stipulate that it is a 19 mm wide PVC tape, and JIS stipulates that it is an approximately 18 mm wide vinyl adhesive tape.
GB and ISO standards stipulate that the sample size is 125 mm × 125 mm. After sewing 12 mm from the edge, cut 6 mm at each end to sew deformation, turn it inside out, and install it on the sample tube, with two samples in each direction of warp and weft. The JIS standard stipulates that the sample size is 10mm×12mm. The sample is wrapped around the sample tube and then sewn with cotton yarn. There are two samples in the warp and weft directions.
GB recommends 7200r for woolen spinning and 14400r for worsted spinning; ISO does not have a unified regulation on the number of rotations; JIS usually sets 10h for woven fabrics and 5h for knitted fabrics. For cashmere knitwear, the usual practice at home and abroad is 7200r for woolen spinning and 10800r for worsted spinning.