Working principle and test process of breathing valve air tightness tester
As an indispensable part of modern industrial quality control, the breathing air tightness tester is increasingly prominent in various fields that require gas sealing performance. Whether it is food packaging, medical equipment, automotive electronics, or aerospace, ensuring the air tightness of the product is a key link to ensuring product quality, extending service life, and maintaining consumer safety.
As a modern technology enterprise integrating R&D, manufacturing, sales, training, and service, Shanghai Qianshi Precision Electromechanical Technology Co., Ltd. is committed to delivering more testing instruments to the market, providing testing instruments for textiles, leather, combustion, automotive interior and exterior trims, material environmental climate aging, etc., and non-standard customization is also acceptable. Before purchase, targeted tests can be carried out according to customer requirements to ensure that the purchased instruments are suitable.
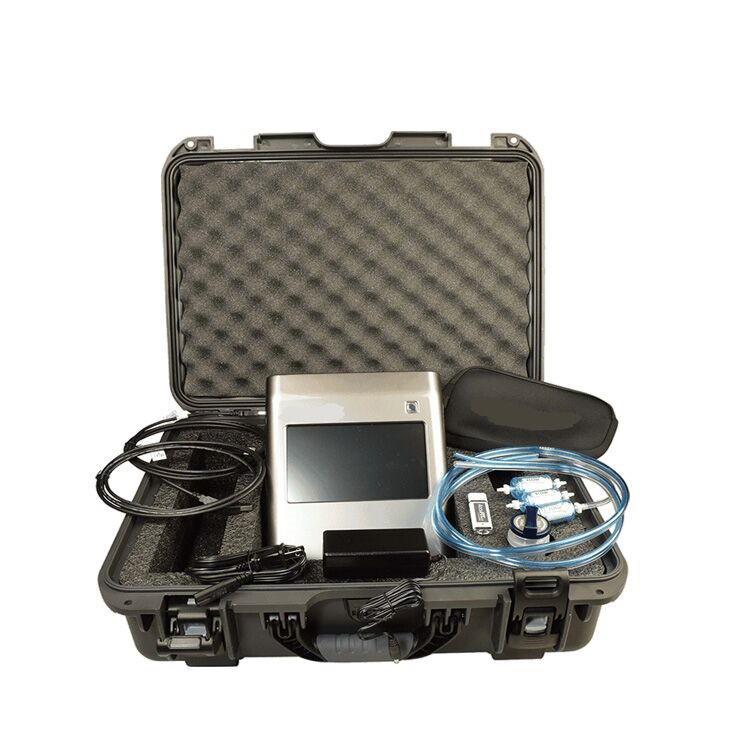
Working principle:
The breathing valve air tightness tester is based on the pressure decay method or the mass flow method for detection. The pressure decay method judges the air tightness by filling a certain pressure of gas into the tested object and then monitoring its pressure change over time; while the mass flow method evaluates its sealing performance by measuring the mass flow of gas exchange inside and outside the tested object. The two methods have their advantages and disadvantages. When choosing, you need to consider the characteristics of the DUT, the test accuracy requirements, and the cost budget.
According to the different test methods, the breathing valve air tightness tester can be roughly divided into positive pressure tester, negative pressure tester, and positive and negative pressure combination tester. A positive pressure tester is mainly suitable for testing containers or components that can withstand a certain internal pressure; a negative pressure tester is more suitable for testing components that need to withstand external pressure or a vacuum environment; and a positive and negative pressure combination tester has both functions and a wider range of applications.
Test process:
1. Preparation stage: Clean the DUT to ensure that there are no impurities such as dust and oil that affect the test results. Connect the tester to the DUT and set the test parameters (such as test pressure, time, etc.).
2. Pre-test: Perform a pre-test to confirm that the tester is in good condition to avoid misjudgment due to instrument failure.
3. Formal test: Start the tester and test according to the set procedure. During this period, the tester will monitor the changes in gas pressure or mass flow inside the DUT.
4. Result analysis: After the test, the tester will automatically or manually display the test results, including leakage rate, whether it is qualified, etc.
5. Record and feedback: The test results will be recorded in the test report, and unqualified products will be marked and fed back to the relevant departments for processing.