Technical advantages of paper clip scratch tester
As a device specially used to evaluate the wear resistance and scratch resistance of material surfaces, paper clip scratch tester plays an important role in materials science, manufacturing and consumer products.
Shanghai Qianshi Precision Electromechanical Technology Co., Ltd. was established in 2012. It focuses on the research, development, design and production of textile testing instruments, and provides textile testing instruments and services for academic research units and testing institutions. Shanghai Qianshi is one of the most competitive and R&D textile testing instrument manufacturers in China. The R&D team is composed of a group of experienced engineers. We are committed to serving customers wholeheartedly and striving to promote technological innovation of textile testing instruments.
Working principle:
The basic working principle is to conduct quantitative and qualitative tests on the surface of materials by simulating the scratching conditions that may be encountered in the actual use environment. During the test, a device equipped with a paper clip (or a scratching head of other shapes and materials) moves along a specified path on the surface of the material at a preset force and speed. During this process, the test machine will record key data such as the force required during the scratching process, the number of scratches, and the degree of damage to the material surface, so as to evaluate the wear resistance and scratch resistance of the material.
It is worth noting that the paper clip scratch tester does not only use paper clips as scratching tools, but the name vividly describes its ability to perform small and fine scratch tests. In fact, according to the test requirements, the scratch head can be replaced with objects of different hardness, shape and material to simulate the scratching conditions in different application scenarios.
Application areas:
The paper clip scratch tester has a wide range of applications, covering almost all areas where the wear resistance and scratch resistance of the material surface need to be evaluated. In the coating industry, it is used to test the hardness, adhesion and wear resistance of the coating; in the automotive industry, it is used to evaluate the durability of the body paint and interior materials; in the field of electronic products, it ensures that components such as touch screens and shells are not damaged during long-term use; in the construction industry, it tests the scratch resistance of floor and wall materials; even in the field of cultural relics protection, it has its place to help evaluate the protective effect of restoration materials on the surface of cultural relics.
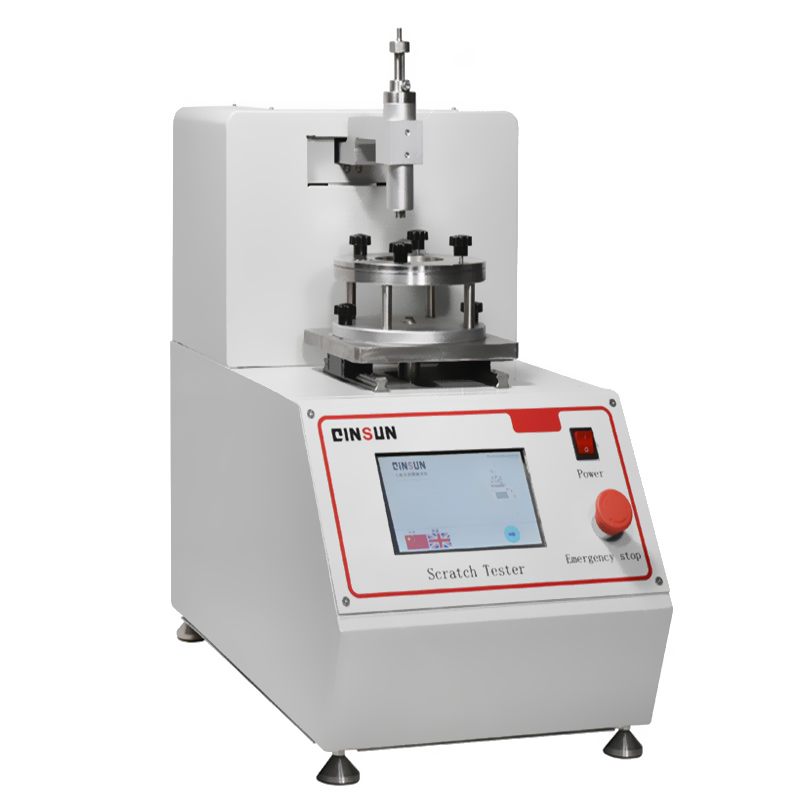
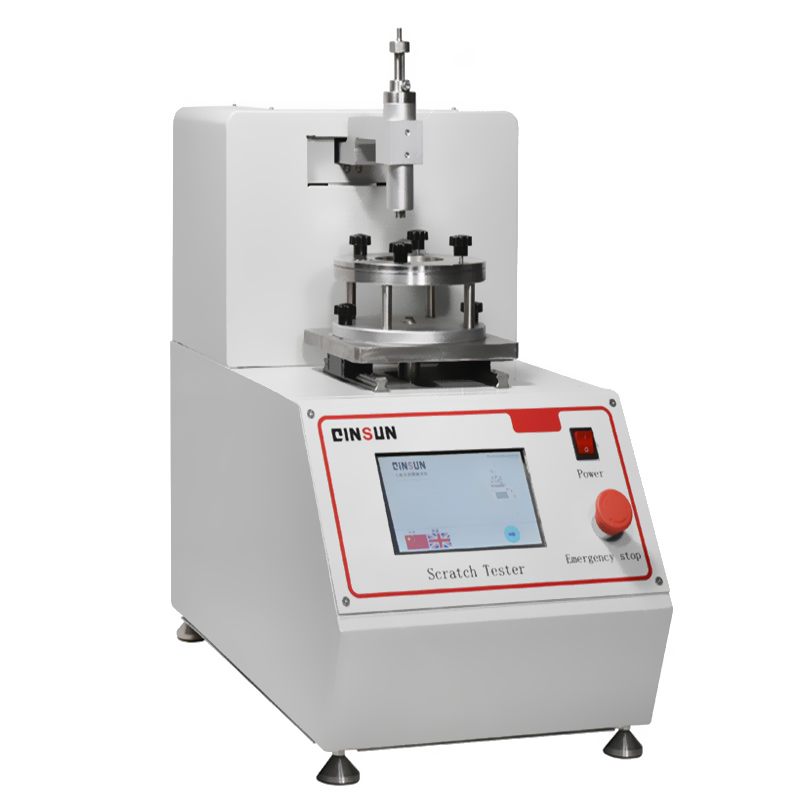
Test standards:
To ensure the accuracy and comparability of test results, the testing of paper clip scratch testers usually follows a series of international or industry standards. These standards specify in detail the test conditions (such as temperature, humidity), test methods (such as scratch speed, force), evaluation criteria (such as damage level classification), etc., to ensure the consistency of the test process and the reliability of the results. For example, international standard organizations such as ISO, ASTM, and DIN have all issued relevant wear and scratch resistance test standards, providing clear guidance for different industries.
Technical advantages:
1. High precision: The use of advanced sensors and control systems can accurately control the scratch force, speed and path to ensure the accuracy of test results.
2. Versatility: By replacing the scratch head and adjusting the test parameters, a variety of scratch scenarios can be simulated to meet the testing needs of different materials.
3. Automation and intelligence: Some high-end models have automated testing and data acquisition functions, which greatly improves test efficiency and reduces human errors.
4. Data visualization: After the test, the testing machine can provide a detailed test report, including the force-displacement curve and damage image during the scratching process, which allows users to intuitively analyze the test results.